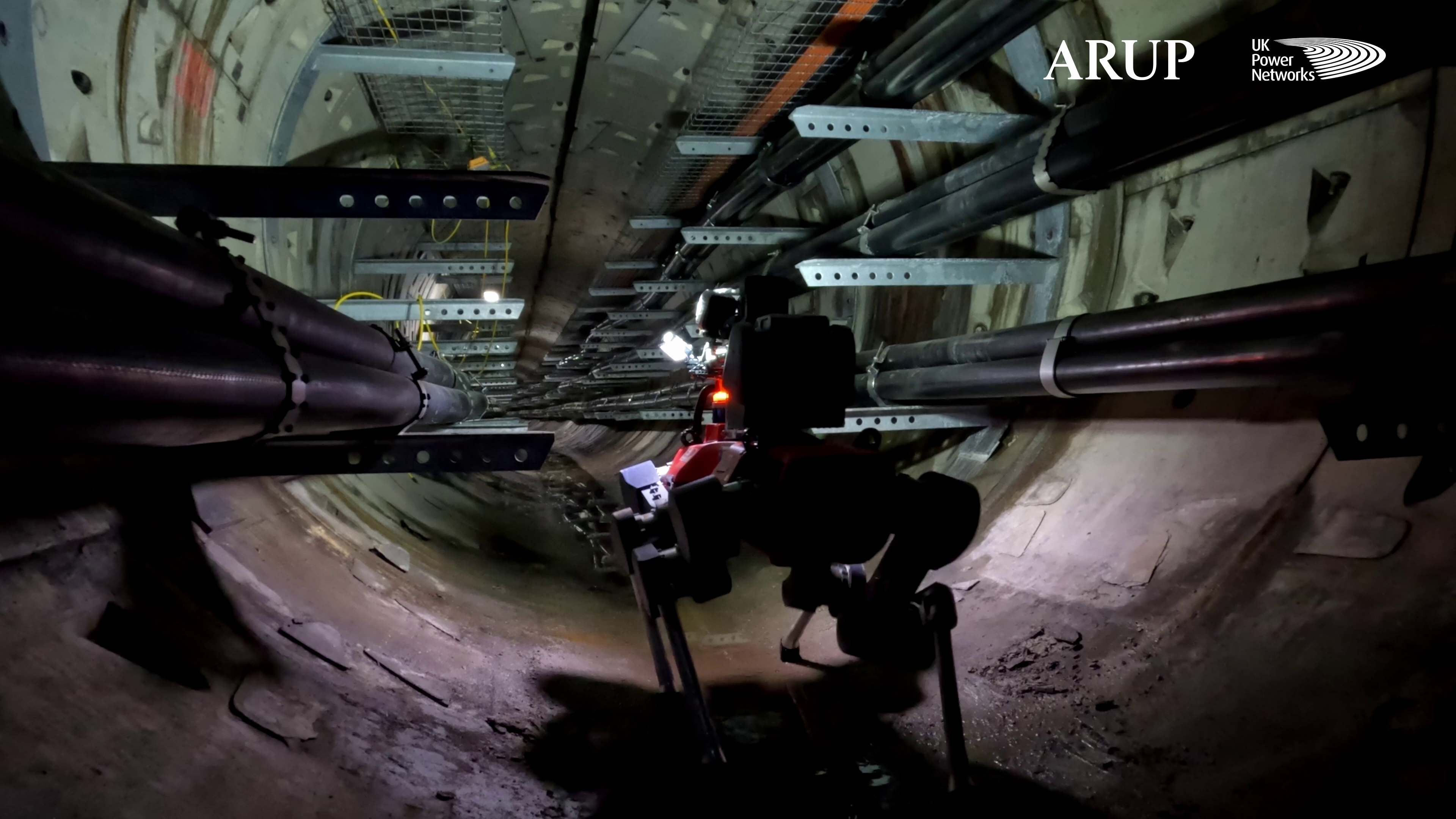
I worked with the infrastructure team at Arup to spearhead an innovative approach to automate and enhance the efficiency of tunnel inspections through the use of 360 imagery, machine learning and robotics.
Tunnel inspections are a time consuming, dangerous, costly and uncomfortable task. By using machine learning and automated capture, it is possible to reduce the risk to human life and greatly improve the reliability and completeness of data capture compared to manual workflows.
You can find a write up of the initial process in this paper.
For the inspection of UK Power Network tunnels, I designed a mounting system for the Anybotics Anymal robot including lighting panels, high capacity battery payload, high output industrial lighting and 360 camera.
The mounting was designed to be modular based on standards used in the film industry eg. the 15mm LWS rod standard used to mount lens supports, FIZ (focus, iris, zoom) systems, batteries and other accessories. My role included designing and sourcing a custom made bent aluminium frame to fit on the robot chassis, wiring hardware, technical drawings and modelling, creating a bill of materials and writing documentation for the client to use when operating the inspection rig.
The entire rig needed to be designed in such a way as to avoid the field of view of the lidar system used for navigation and allow for the free rotation of the official Anybotics pan-tilt inspection payload.
The entire rig needed to be designed in such a way as to avoid the field of view of the lidar system used for navigation and allow for the free rotation of the official Anybotics pan-tilt inspection payload.
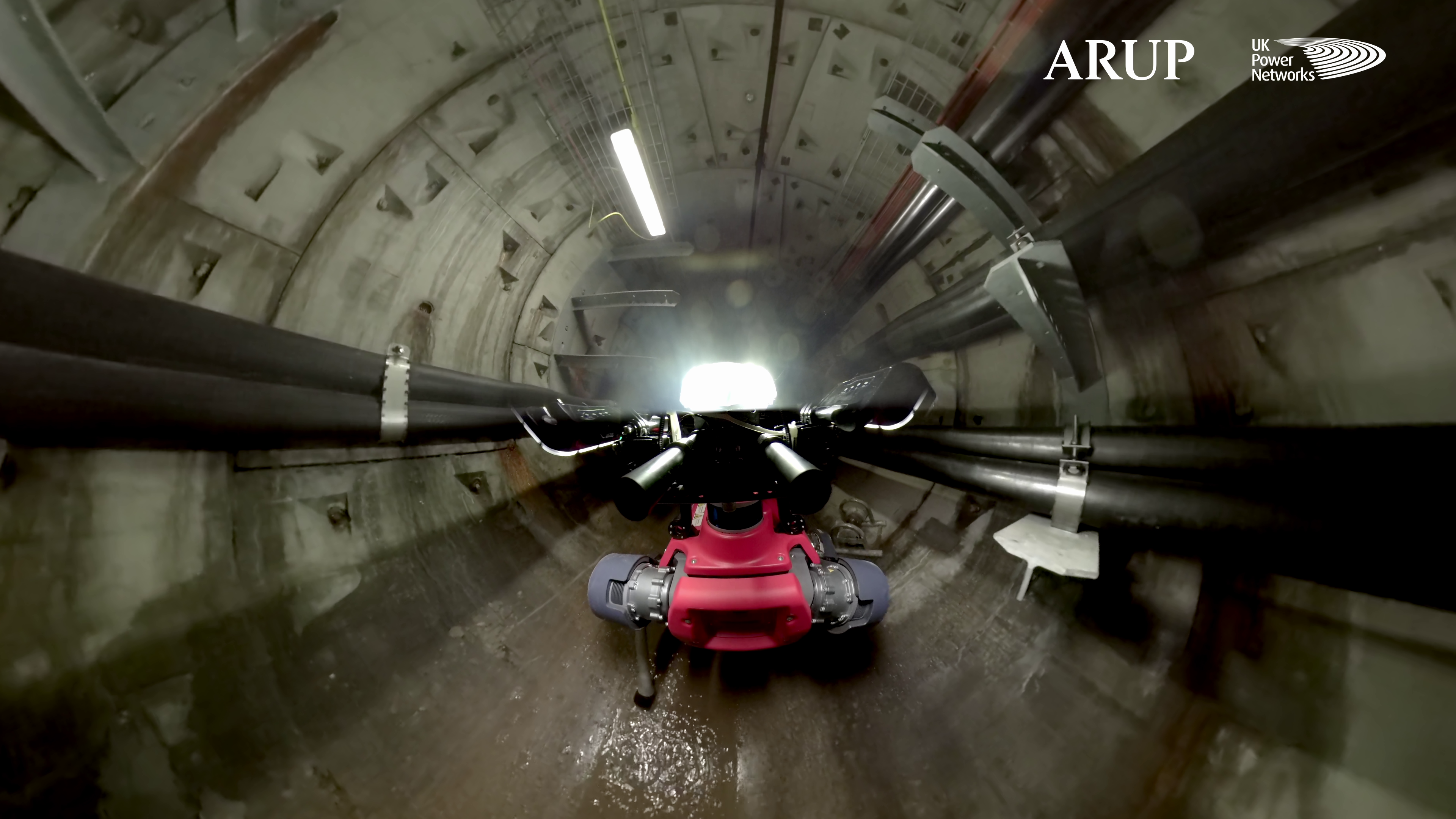
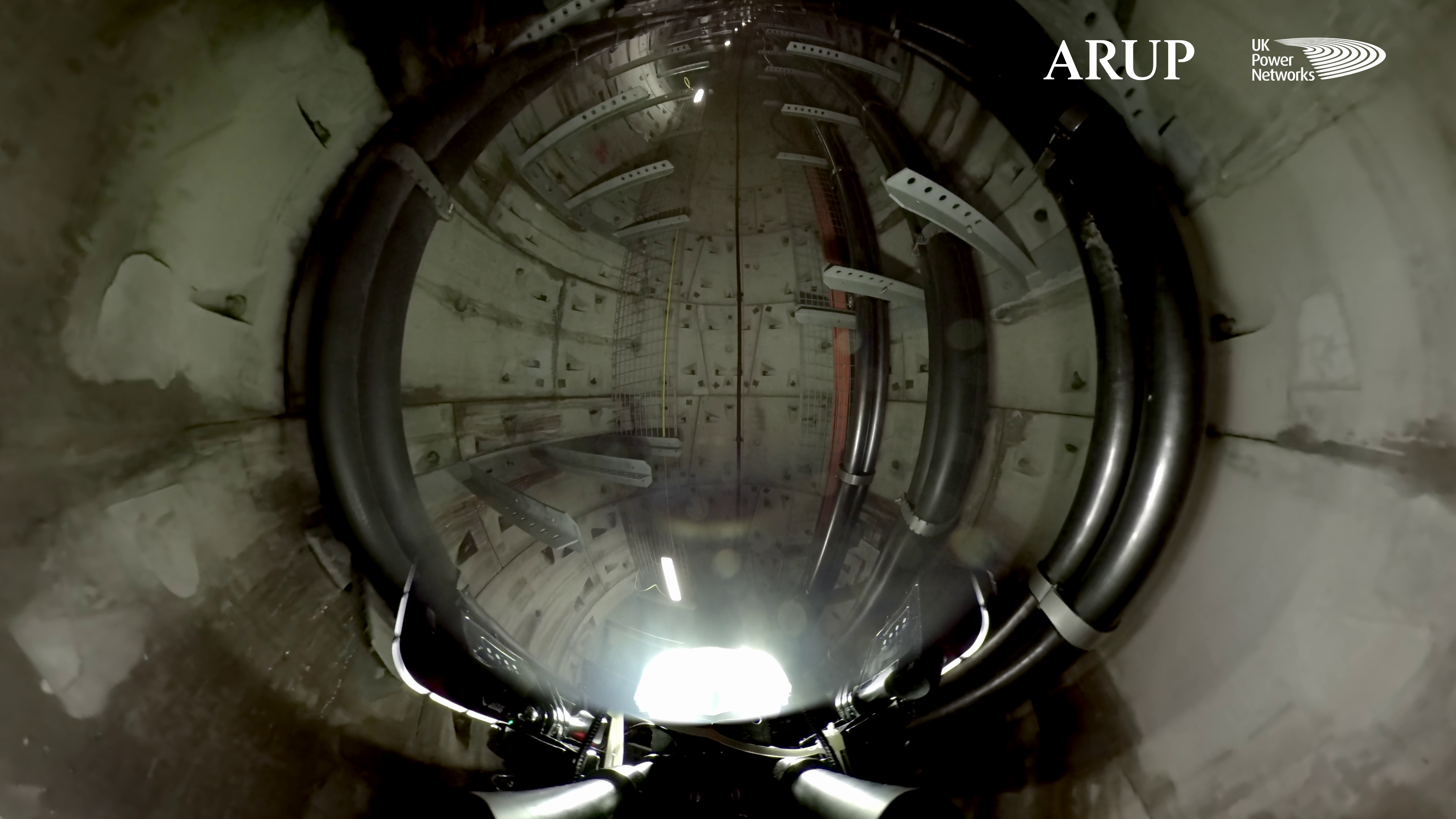
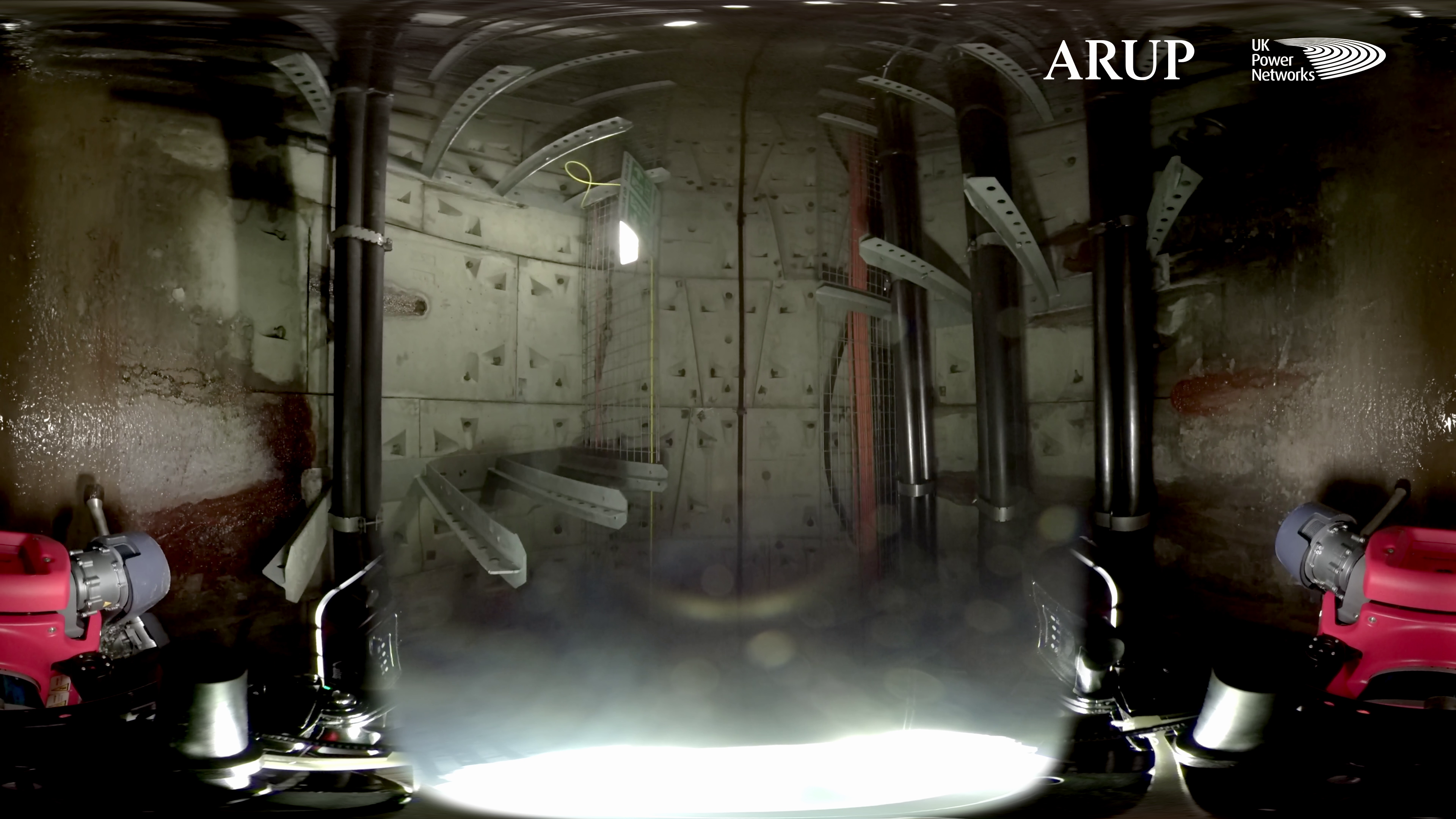
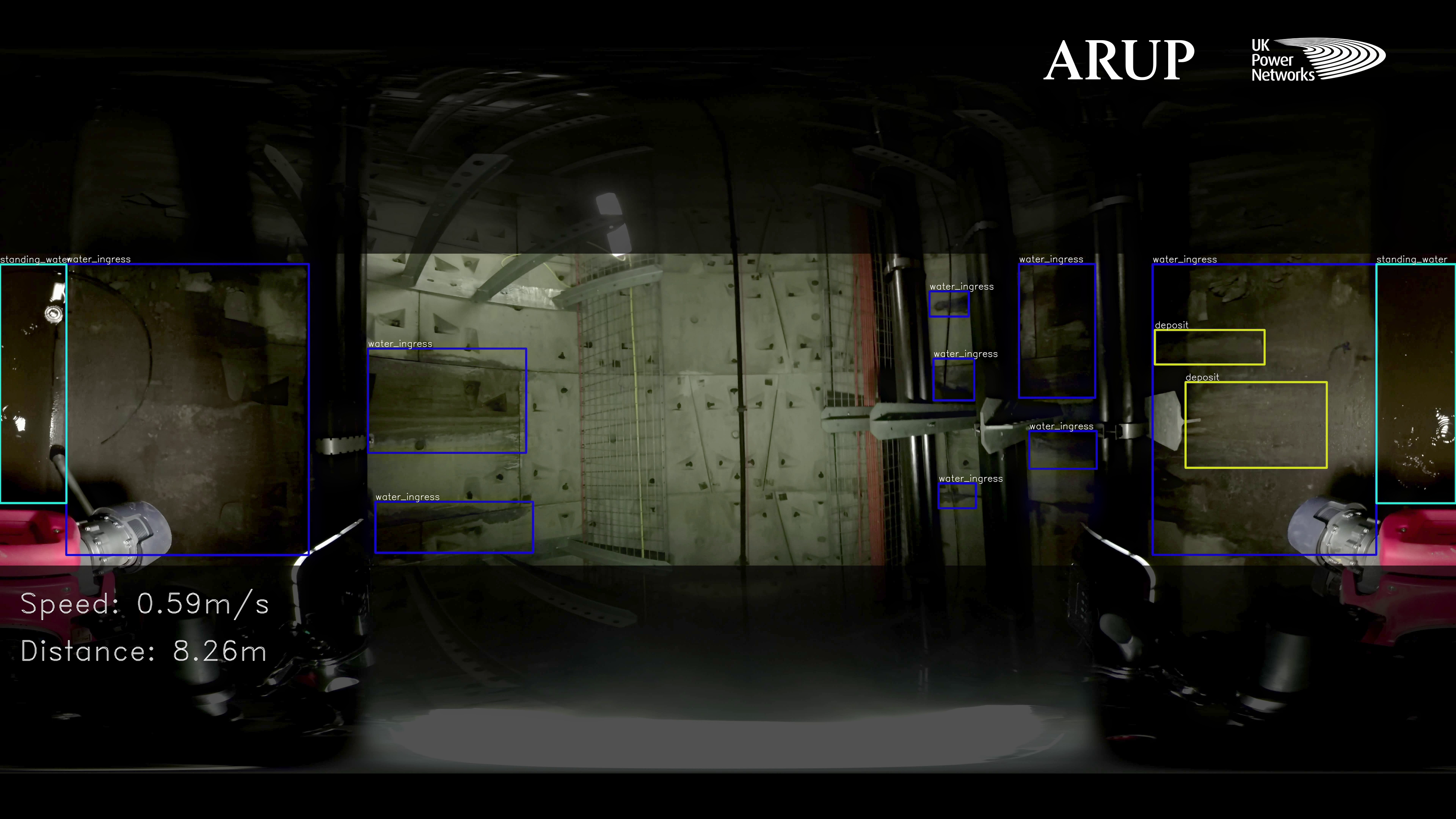